

The Roland Modela 3-Axis Desktop mill in the woodshop is an example of this type of machine.
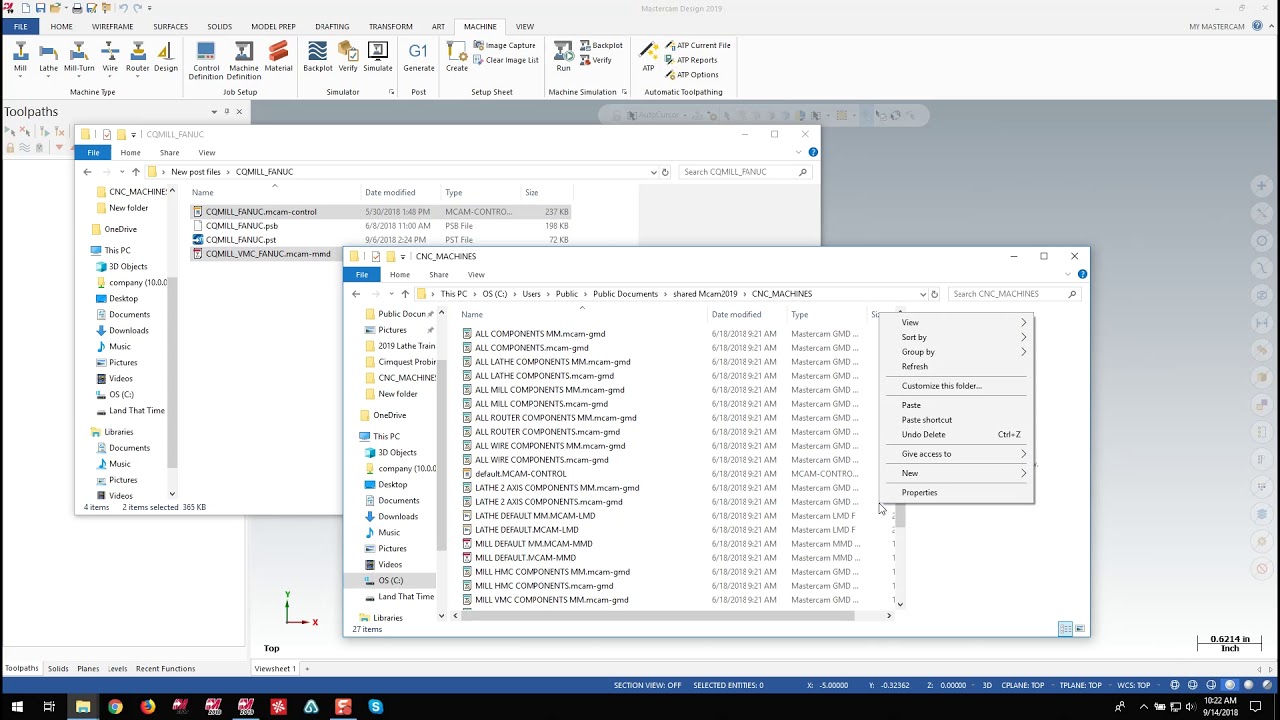
Template file for mastercam 2019 software#
Some CNC milling machines come with proprietary software that can make the process as simple as: importing a mesh surface, making a few decisions regarding desired part resolution, and then hitting "go" on the machine once you've secured the material. Software that generates toolpaths for 3-axis CNC routers and mills will generally work with surfaces, meshes, curves, and points, depending on the particular motion that is being created for the machine. There are a number of different software tools that can create toolpaths from geometry (some require a closed mesh model, like an STL file to a 3D Printer, others work only with 2D curves, like a DWG file for a laser cutter). I may be doing a VTL part, 5 axis Trunnion, 5 Axis head head, or 2 axis lathe, and making templates for all of that would not be profitable.The geometry that you create in Rhino or another 3D modeling program of your choosing will ultimately control the motion the cutting tool takes through the material to make your part. If we were locked into a template method here i would have thrown this computer through the wall.

I am working along and some levels will not be visible or not show up and then I have to open and close the levels manger just I was using V9 most days. One having 2 operation and one have 15 operations pigeon holing us would create more work in a lot cases. we may be making a program for a 2" part and then for a 55" part. We import out items needs, but we do not do families of parts here. He follows the level method I want, and he does a very good job and doing things. In bigger shops I have done this, but myself and the guy I am training are the only 2 guys here. Roger I here what you are saying, but in an environment where you are doing turning, 3 axis, 4th axis, 5th axis, and Mill/turn work you would have to have so many different templates it not becomes more work in simple jobs. All of this adds up to consistency, organization, and minimizing the time wasting things you do on every job. there are many other scenarios like for router customers with a drill block, you can have a template file for when you have different drills loaded into your drill block.Ĩ.
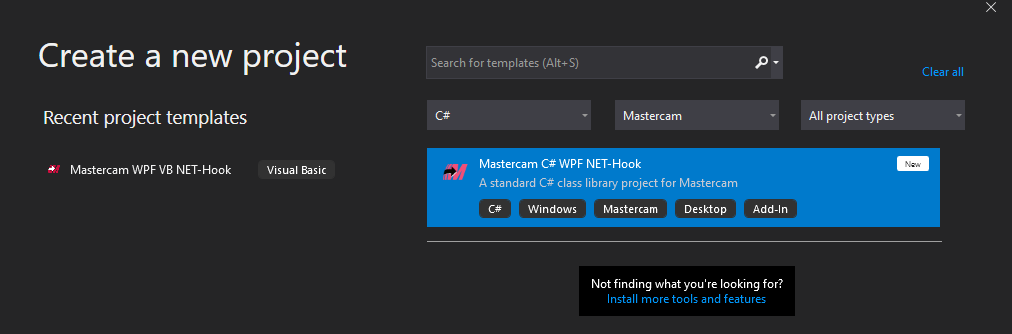
tooling, in addition to the common toolpaths you can have all the tooling predefined in your mcx file with the correct feeds and speeds defined for this style of part/material.ħ.
Template file for mastercam 2019 iso#
little things like G54, G55, G56 notes created in the iso cplane ready to be used for setup sheets. Again if you use 4 vises you could have the vises already setup to accept your merged in geometry. your custom print borders for all the standard size papers you use, just turn a level on. your template file can also contain geometry. For example, if you work with 4 vises you can have four predefined views where all you have to do is set the origin. predefined associative views that can be edited for multiple vises, indexer work, tombstone work, etc. ready to go in the correct toolpath groups refrencing the correct WCS, just add geometryĤ. you can also have the common toolpaths used for this family of parts including tooling, feeds/speeds, stepovers, etc. Example if you have 4 vises you can have a toolpath group for each vise, subgroups for roughing, finishing, drilling, etc.ģ. organized operations manager with group/subgroup names setup for this family of parts. It's a lot faster and easier on every file if you have a consistent set of levels in every file, this is a HUGE timesaver.Ģ. then merge your part geometry in to the existing file.ġ. If you are not familiar with a template file, basically you open an existing mcx file that contains commonly used toolpaths, tooling, levels, views, geometry, etc. The reason for template files are numerous but basically, Template files = faster and easier. In an effort to work smarter (or I'm a little lazy) I've been using template files in Mastercam since V5.5.
